Worm Gear Design Calculation Pdf Viewer
- Gear Calculation Formula Pdf
- Worm Gear Design Calculation Pdf Viewer Software
- Worm Gear Design Calculation Pdf Viewer Download
- Worm Gear Design Formula
- Worm Gear Design Calculation Pdf Viewer Free
- >
(1) Internal Gear Calculations Figure 4.4 presents the mesh of an internal gear and external gear. Of vital importance is the working pitch diameters(dw) and working pressure angle (αw). They can be derived from center distance (a) and Equations (4.3). Table 4.6 shows the calculation steps. It will become a standard gear calculation if x1=x2=0. Gear design in MDESIGN gearbox March 2012 - DriveConcepts GmbH, Dresden 3.2. Design of spur gears Spur gear can be modeled similar. Choose in the element explorer “Gear” “Spur gear” “External gear” and drag it into the 3D-view. Then select it to specify the bevel. Figure 15: Specifications of the bevel.
What is a gear calculator ?
The gear calculator is a comprehensive software which, after inputting various parameters related to gear calculations, computes on-line automatically gear sizes, strengths, working forces, tooth forms, backlash conversions, etc. Because gear calculations require many complex formulas related to strengths and sizes, traditional gear design situations require highly specialized knowledge and suitable design time. By utilizing the gear calculator introduced here, it is possible to reduce these burdens substantially. Among the parameters requiring user input are the unit to specify gear tooth such as module or diametral pitch (DP) and its value, pressure angle, helix angle, number of teeth, coefficient of profile shift, center distance, material, rpm (rotational speed), face width, safety ratio, circumferential backlash, etc. This gear calculator software also handles gear calculations of various types of gears such as spur gears, worm gears, gear racks, bevel gears, internal gears, screw gears, etc.
What is a gear drawing software ?
The gear drawing software means an on-line automatic program to produce gear drawings when users input various parameters needed to define gear sizes. It also allows downloading the produced original (custom) gear drawings in the dxf format and expands them by using CAD software. Without this kind of dedicated gear drawing software, it would be necessary, after gear sizes have been determined, to use conventional CAD software and draw the gears from scratch. Therefore, the use of this kind of gear drawing software allows large scale improvement in gear designs. Among the parameters requiring user input are the unit to specify gear tooth such as module or diametral pitch (DP) and its value, standard cross section of the tooth, coefficient of profile shift, precision grade such as JIS, hub diameter, bore diameter and its tolerance, size of the chamfer, various sizes related to keyway, number and positions of tapped and counterbore holes, etc. As with the gear calculator, this gear drawing software also handles making drawing of various types of gears such as spur gears, worm gears, gear racks, bevel gears, internal gears, screw gears, etc.
GCSW - Free Gear Calculator
Spur GearsWorm Gears
Bevel Gears
Rack and Pinion
Screw Gears
Internal Gears
To register to use this calculator, click here
To check your registration status, click here
GDSW - Free Gear Drawing Software
Spur GearsWorm Gears
Bevel Gears
Gear Rack
Screw Gears
Internal Gears
To register to use this calculator, click here
To check your registration status, click here
Example of the Parameter Input Screen of this Gear Calculator :
As an example, we will introduce the parameter setup screen for the bending strength calculation of spur (or helical) gears.
1.
In this section, we input the tooth size.
For the unit of the tooth size, you can choose the international standard of module, inch based diametral pitch (DP) or circular pitch.
For the tooth's standard cross section, it is possible to select the normal to the tooth or perpendicular to its shaft.
2.
In this section, we can input pressure angle normal to the tooth, tooth's twisting angle, addendum and dedendum coefficients. /p90x-ab-ripper-x-video-download.html.
3.
Here, you input the number of teeth of the pinion and the gear.
Also, you can input each coefficient of normal profile shift of the gears.
Besides the strength calculation, this gear calculator can also compute sizes, forces acting on the teeth, tooth forms, etc.
However, for this example, we will focus on the required parameters for strength calculation (bending strength).
For strength calculation, you can compute the bending strengths and gear surface durability.
For MC Nylon gears, only the bending strength calculation is available.
In this section, we input the parameters associated with the gears' actual usage environment.
4.
Input the center distance between the pinion and the gear.
5.
If needed, also input the gear cutting tool's tip rounding radius coefficient.
6.
Input the number of teeth of the pinion and the gear.
7.
Enter the precision grades of the two gears as well as absence or existence of tooth form correction(s).
8.
Here you can select the materials of the two gears such as S45C, SCM415, SCM440, etc. In addition, selection of surface hardness such as induction hardening, carburizing, nitriding, normalizing, hardening and tempering, etc. can be made. Also, detailed settings of hardness of center (HB)(HV), tooth surface durability (HB)(HV), allowable bending stress (σFlim), allowable Hertz stress (σHlim), etc. are possible.
9.
Input the rotational speed (rpm) of the pinion here.
10.
Here you enter the number of repetitions.
11.
It is possible to enter the safety factor here.
12.
Enter the overload coefficient.
13.
It is possible to select the unit of force in kgf or Nm.
14.
As soon as the parameter entries have been completed, press this button to display the results of the calculations.
Example of Results of the Strength Calculations (Tooth Bending Strength Calculations) for Spur and Helical Gears
Gear Calculation Formula Pdf
15.
Allowable torques (Nm) for the pinion and the gear respectively are displayed based on the strength calculations.
Other Functions
Calculation of force acting on gears
Backlash conversion
DISCLAIMER
This software is provided as an exclusive service to our registered users.
The contents of the software may be revised for improvements without notice.
Any damages directly or indirectly suffered by the users of this software are the responsibility of the users and we do not offer any compensation.
We are not responsible for your loss of data from system malfunctions.
Calculation results such as values of strength are not guaranteed values. Please use them as reference values.
This software is protected by copyright law. You are prohibited from changing or copying the contents without writtten consent from us.
For customers without SSL :
In order to avoid interception of our customer's important information, our software has high security settings.
Please contact your system administrator if you have problems opening GCSW, GDSW or the comment form.
We ask for your understanding that we cannot respond to these issues.
WORM GEAR
Common terms used :
The following terms, in connection with the worm gearing, are important from the subject point of view :
1.Axial pitch. It is also known as linear pitch of a worm. It is the distance measured axially(i.e. parallel to the axis of worm) from a point on one thread to the corresponding point on the adjacent thread on the worm, as shown in Fig. 31.3. It may be noted that the axial pitch (pa) of a worm is equal to the circular pitch ( pc ) of the mating worm gear, when the shafts are at right angles.
2.Lead. It is the linear distance through which a point on a thread moves ahead in onerevolution of the worm. For single start threads, lead is equal to the axial pitch, but for multiple start threads, lead is equal to the product of axial pitch and number of starts. Mathematically,
Lead, l = pa . n
where pa = Axial pitch ; and
n = Number of starts.
3. Lead angle. It is the angle between the tangent to the thread helix on the pitch cylinder and the plane normal to the axis of the worm. It is denoted by λ.
Worm Gear Design Calculation Pdf Viewer Software
A little consideration will show that if one complete turn of a worm thread be imagined to be unwound from the body of the worm, it will form an inclined plane whose base is equal to the pitch circumference of the worm and altitude equal to lead of the worm.
DW = Pitch circle diameter of worm.
The lead angle (λ) may vary from 9° to 45°. It has been shown by F.A. Halsey that a lead angle less than 9° results in rapid wear and the safe value of λ is 12½°.
4. Tooth pressure angle. It is measured in a plane containing the axis of the worm and is equal to one-half the thread profile angle as shown in Fig. Normal pitch. It is the distance measured along the normal to the threads between two corresponding points on two adjacent threads of the worm.
Mathematically,
Normal pitch, pN = pa.cos λ
Note. The term normal pitch is used for a worm having single start threads. In case of a worm having multiple start threads, the term normal lead (l N) is used, such that
lN = l . cos λ
6. Helix angle. It is the angle between the tangent to the thread helix on the pitch cylinder and the axis of the worm. It is denoted by αW,. The worm helix angle is the complement of
worm lead angle, i.e.
αW + λ = 90°
It may be noted that the helix angle on the worm is generally quite large and that on the worm gear is very small. Thus, it is usual to specify the lead angle (λ) on the worm and helix angle (αG) on the worm gear. These two angles are equal for a 90° shaft angle.
7. Velocity ratio. It is the ratio of the speed of worm (NW) in r.p.m. to the speed of the worm gear (NG) in r.p.m. Mathematically, velocity ratio,
V.R. = Nw / NG
Let l = Lead of the worm, and
DG = Pitch circle diameter of the worm gear.
We know that linear velocity of the worm,
vW = l . NW/60
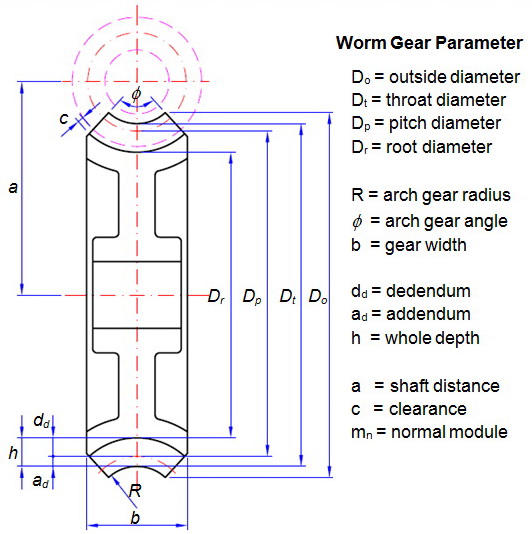
where n = Number of starts of the worm.
DESIGN PROCEDURE FOR WORM GEAR:
1.Selection of the material:
2.Calculation of teeth:
üAssume Z1 depending upon the number of stat.
üZ2 = i X Z1
3.Calculation of diameter factor and lead angle
q = d1/mx
If not given assume q= 11
ɤ= tan-1 (z1/q)
4.Calculation of Tangential load:
Ft = (p/v) x K0
5.Calculation of Dynamic load:
Worm Gear Design Calculation Pdf Viewer Download
Fd = Ft / cv
6.Calculation of Beam strength:
Fs = π mx b [ϭb] y
7.Calculation of Axial load:
Calculate axial load by equating Fd and Fs
8.Calculate b, d2, v.
9.Recalculation of beam strength
Fs = π mx b [ϭb] y1
10. Recalculation of dynamic load
Fd = Ft / cv
11. Check for beam strength:
If Fd ≤ Fd, design is satisfactory.
12. Calculation for maximum wear load:
Fw = d2. b . Kw
13. Check for wear strength:
If Fd ≤ Fw, design is satisfactory./ableton-live-lite-4-behringer-download.html.
Worm Gear Design Formula
14.Calculate power loss and area:
Worm Gear Design Calculation Pdf Viewer Free
15.Calculate basic dimensions.